What Does Dmg To Pine Walls
Dec 30, 2016 Here's a possible design idea to keep the wood look but update it. Lightly sand 2-3 panels and stain a darker color to give an overall stripped wall of wood. Just a thought. I do like the knotty pine and would keep it intact for now. Never know when that total wood look is going to come back around! When living in older homes, make the most of what you have - decades-old fixtures such as a wall-mounted ironing board and wall treatments such as knotty pine paneling. Decorating with knotty pine dates back to the 1950s when it was used for basement rec rooms and upstairs dens, and the wood is known for its vertical grain speckled with tiny.
- POST a QUESTION or COMMENT about the diagnosis & repair of wood floors
Jul 16, 2018 Have knotty pine paneling in your home and not sure what to do with it? Before you paint over it or tear it out, try these knotty pine walls decorating ideas – it just might make you love that paneling after all. The Birch Wall is a Common Structure in Unturned 3. It can be placed between two Pillars. Blueprints: Birch Log (x3)= Birch Wall The Maple Wall is an Uncommon Structure in Unturned 3. It can be placed between two Pillars. Blueprints: Maple Log (x3)= Maple Wall The Pine Wall is a Rare Structure in Unturned 3. It can be placed between two Pillars. The Pine Wall is a structure in Unturned 3. Feb 17, 2011 Click on link to learn more about remodeling, drywall and other ways that you can save money, by preventing damage to your.
InspectAPedia tolerates no conflicts of interest. We have no relationship with advertisers, products, or services discussed at this website.
This article explains types of damage that occurs on various types of wood flooring in buildings.
We illustrate buckling wood floors and comment on how they happen; we illustrate cupping of wood flooring and point out the diagnostic value of noticing which way the cup is shaped.
We explain what to do about gaps between interior floor boards, and we also address deterioration and problems with outside wood decks and porch floors, and we also describe repair approaches for various wood floor damage.
We also provide a MASTER INDEX to this topic, or you can try the page top or bottom SEARCH BOX as a quick way to find information you need.
A Photo Catalog of Damage to Wood Floors
Repair approaches for damaged wood floors
- WOOD FLOOR DAMAGE REPAIR
Buckled wood flooring due to leaks or high moisture
Our photo at page top shows cupped wooden strip flooring and an easy way to detect this condition.
This 1940's wood floor buckled severely because of wet conditions in a gymnasium after the roof leaked.
But even if a building is not subjected to flooding or wet floors, if the wood floor was installed without adequate clearance around its perimeter buckling can occur when moisture increases in the building.
And as we discuss at FLOOR, WOOD MOISTURE, a successful wood floor installation requires that the wood flooring be acclimatized and at proper moisture level in the building before it is installed.
Very large wood floors (such as in this gym) may need an inch or even more of side clearance at the building walls - a detail accomplished by building out floor/wall baseboard trim if necessary, or in the case of newer products, by the combination of clearance gaps and a floating floor design.
Cupped Wood Flooring - Causes & Cures
Compare our photo concave (curved down) cupped wooden floorboards with the convex (curved up) cupped floor boards in the photo at the top of this page.
At left you can easily see the concave cupping of the floor at left by looking at our flashlight beam across boards in the upper portion of the photo.
(The center of concave cupping is down and edges of concave-cupped floor boards are raised - think of 'cave' as 'caving in' if you want to remember this distinction.)
Diagnosing why a wooden floor has become cupped is an important step in correcting the problem, since we need to identify and correct the moisture source.
There are exceptions, but in general a board swells on its side that is most moist.
So on an interior floor like the one shown at left, the fact that the center of the floorboards is cupped 'down' we infer that it is the down-side of these boards that is more moist than the finish side facing the room.
We find this condition in homes with finished wood flooring installed over a damp or wet basement or crawl space.
To protect wood floors over crawl spaces from moisture damage see
- NAHB, ICC & ICC Evaluation Service, FLOORS ABOVE CRAWL SPACES: Reducing the Risk of Moisture Accumulation with Wood Floor Assemblies for Residential Buildings in Hot-Humid Climates [PDF], (2014) retrieved 2018/03/17, original source: https://www.homeinnovation.com/~/ media/Files/Reports/ TechNotes-Floors-above-Crawl-Spaces-June-2014.pdf
At our page top photo the finish floor boards seem to be cupped 'up' - suggesting that this floor has been wet from above.
If the floor board cupping is minor and hard to see, you might decide to just address the moisture problem and leave the floor alone.
It won't recover, but it the floor should not get worse. How would we repair a badly cupped wooden floor?
Sanding the floor flat is an option unless the boards have not only cupped but come loose from the subfloor. In that case floor replacement may be necessary.
Cause of Outdoor Deck Board & Stair Tread Cupping & Shelling - Bark Side Down Advice for Decks & Steps
Indoors we find that floor boards tend to cup so that the concave side of the board is towards the floor's more dry side, and the convex side of the cupped or curved boards tend to be facing the floor's more wet side.
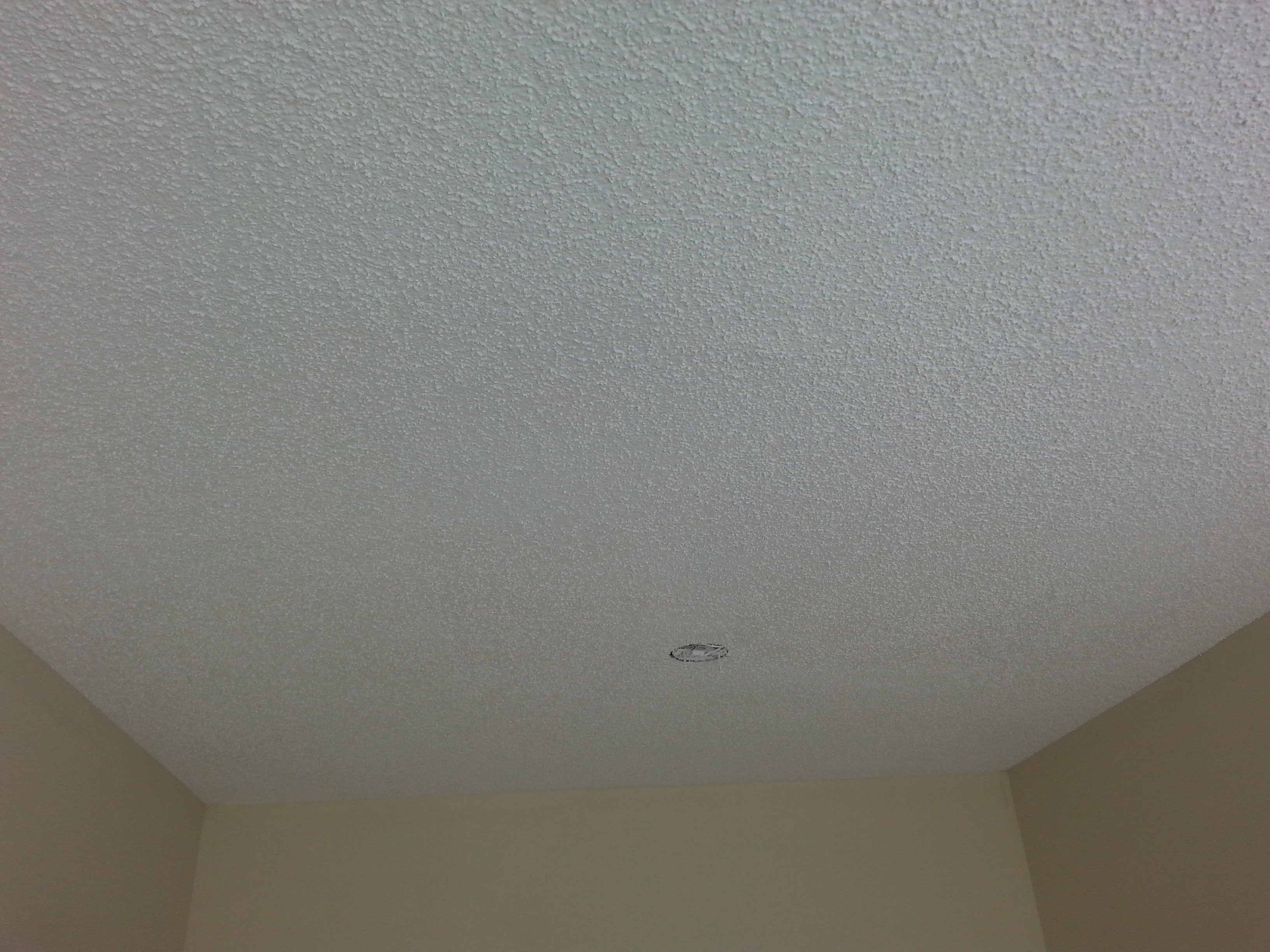
Apparently when a wooden board has uneven moisture content across its thickness it will tend to expand more on its more wet side, causing that side to 'arch' or become convex.
You might think that outdoors where despite temporary wetting from rain, deck boards and wood step boards open to air on both sides ultimately have a uniform moisture content across the board's thickness.
But because the upper board surface is exposed to sun and in some cases more wind or air movement, the under-side of boards may have a higher moisture content. In some installations, significantly higher.
For an explanation of wood board cupping and which side of deck, ramp, and exterior stair boards should face 'up'.
See BARK SIDE UP on DECKS & STEPS.
Cupped ramp boards (or deck and platform boards) with the 'cup' facing up will hold water and form algae or ice more quickly than boards that drain properly, increasing the risk of a slip, trip, or fall hazard. Upwards-cupped boards sometimes rot faster too .
Look at the end-grain of any deck, ramp, or wooden walkway board and notice the curved lines that mark the winter wood layers of the tree from which the board was cut. If these lines arch 'upwards' when the board is placed, most boards will also be curved upwards (convex) and will drain better.
But before nailing a deck or ramp board in place, look at the board surface itself - sometimes the boards don't follow these 'cupping rules', or the bark side of the board may be badly damaged - so when building a wood structure you may have a reason to place a few walking-surface boards 'upside down'.
(Sketch adapted from (flipped over) an original provided courtesy S. Bliss, Best Practices in Residential Construction.)
When building a deck we like to look at the end grain of the wood and install deck boards with the 'bark side' up so that cupped boards won't form puddle-collecting dips on our deck.
But look at your actual individual boards or stair treads when you are building an outdoor structure. If we are installing a deck board that is already rather cupped, we install it with the convex or 'outward curve' side facing up for best drainage.
- See BOARD CUPPING CAUSES
- Also see DECK & PORCH CONSTRUCTION.
Watch out for shelling, board wear, trip hazard:
Watch out: On wooden decks and stair treads a defect 'shelling' can occur with the bark side down method.
Shelling is a term used by some builders to refer to the loss of portions of a board surface as late wood growth (the outer surface of the tree and thus the 'bark side' of the board) separates from early wood growth (the inner portion of the tree or the tree-center side of the board).
Shelling is reported to occur more often in lumber made from Douglas Fir and Southern Pine. When building an outdoor deck wooden stair tread, it is a good idea to avoid using boards with questionable, likely to separate, portions of their upper surface.
Shelling may be less of a problem with wood trim that is to be placed vertically and kept painted or sealed. We discuss shelling further
at SHELLING DAMAGE TO WALKING SURFACES ON WOOD DECKS & STAIRS.
Just check the things you want to remove, and then click the Clean button.Clear Out Temporary FilesYour Mac’s hard drive probably has temporary files you don’t need. You’ll probably want to close iTunes before you do that./Library/Application Support/MobileSync/BackupThe easier (and much safer) way to delete them is to use, which translates those confusing folders into actual backup names so you can decide which backup you actually want to delete. These files often take up disk space for no good reason. Dmg taking up installation space.
Gaps Between Wood Floor Boards & in Parquet Flooring: Cause & Cure
Gaps between wood floorboards may occur for several reasons, but the common underlying cause is a moisture problem.
Installing wood flooring before it has had an opportunity to acclimate to the indoor moisture level of its new home often means that too-moist flooring was nailed in place, later shrinking as building heat further dries the wood.
The gap between the flooring shown at left is viewed from the under-side of the floor of an older building. This is a ship-lap joint whose boards have separated about 3/16'.
Gaps can also appear between sections of a wood parquet floor, as shown in our photo (left).
Watch out: Do not rush to fill in gaps like this in wooden floors. Particularly in the case of wideboard flooring the width of individual boards increases and decreases seasonally as building indoor moisture levels increase (typically in the summer) or decrease (typically in winter).
If you fill the gap between floor boards in the dry (wide gap) season, when the building moisture increases and boards swell the swelling floor boards will push against the gap filling material, actually crushing the edges of the floor board.
Then when the building dries out again a new gap will appear. Or in extreme cases the floor may buckle in damp weather. In either case, it's better to just vacuum out the dust and debris and leave these wideboard floor gaps alone.
At WOOD FLOOR TYPES where we illustrate a restored and re-finished wide-board floor in an 1860's home, if you click and enlarge the photo you'll see that we left the flooring gaps open. In fact during restoration we sometimes have to pick out putty or other stupid crack fillers that someone has applied earlier.
Gaps and shrinkage damage to wood floors installed over radiant floor heating systems
A common complaint we've investigated is shrinkage gaps in wood flooring installed over radiant heat tubing.
The underlying cause may be flooring that was too moist at installation (see above), or operating the heat at a higher than recommended temperature.
In the gapped wood floor over radiant tubing shown here, the owner, attempting to eliminate a smell associated with the radiant heat tubing, ran the heating system at high temperature, perhaps contributing to this floor gap problem.
See these articles on radiant heated floors
- FLOOR, WOOD RADIANT HEAT - guide to installing wood floors over radiant heat system
- WOOD FLOOR DAMAGE - from radiant tubing run too hot
Loose or Squeaky Floorboard Diagnosis & Repair Suggestions
Reader Question: 3/23/2014 Nick Ellicott City said:
The floors I need help with have loose boards, gap at the top step tread and the house doesn't have air conditioning.
The floors were laid in 1939. Would subflooring have been laid this long ago and is that why there are loose boards and is very squeaky in places? No pet stains, no dark spots should I sand or just fill with sawdust slurry and oil.
[Click to enlarge any image] Shown at left, an older wood floor in Rockefeller Hall, Vassar College - DF.
Reply: use sawdust to fill wood floor gaps?
Nick I'm unclear on what we're discussing here, so can only make some guesses.
What Does Dmg To Pine Walls Paint
By 1939 many homes had wood floors installed over wood subfloor - the way to find out is to examine both sides of the floor, but one can also often infer or guess or discover the floor structure just from the top surface by noticing the floor type (wideboard vs. newer solid oak or pine narrow board flooring) and by probing gaps between floor boards to see if a subfloor is encountered.
The 19th century wideboard pine floor shown below was installed directly to joists.
About using sawdust to fill wood floor gaps
What Does Dmg To Pine Walls Cost
I would not fill gaps in wood flooring with sawdust and oil nor anything else, both because I'm uncertain about odor and fire safety issues from the mixture you describe and because gaps in wood floors vary in width seasonally as temperatures and moisture change.
Filling gaps between wood floor boards invites later buckling or causes further compression of the edges of boards when they next expand.
You can see that's what's been happening with the putty-filled wood floor gaps in photo at left.
See GAPS BETWEEN FLOOR BOARDS for details.
Follow-Up:
Thanks. I will examine the underneath and see if there is subflooring. They are very squeaky in some places.
Can I nail down the squeaky areas? I saw the sawdust on a Youtube video. This is my first DIY project, do you suggest hand sanding? I also saw cleaning the floors with vinegar. The finished stain color is ideal. I don't want to do too much and ruin them. Your thoughts.
Reply: How to repair a squeaky wood floor
Squeaky wood floors are caused by movement in one or more boards that rub together as you walk over them or as building temperatures and moisture level change.
Ideally we repair loose wood flooring by screwing up or nailing-up from beneath the floor, through the subflooring or best on an angle through the floor joists, through the subfloor (if present) and into the bottom of the finish flooring above.
Nick, at LOOSE NOISY FLOOR REPAIR I've collected a complete set of steps for repairing loose or noisy wood flooring working from above or from below depending on the situation.
Sanding old wood floors: advice
About hand sanding versus power sanding, the answer is, as Mark Cramer says, .. it depends.
On a hardwood floor with plenty of wood thickness and deep damage we might use a power sander along with an edger.
On an antique (often soft-wood) floor like the one shown at left we use a combination of sharp hand scrapers and hand sanding. In my opinion sanding an antique or historic floor dead flat produces a weird and inappropriate finish.
In general using the least destructive, least invasive method is best.
Mold & Other Stains or Mold Damaged Wood Floors
See MOLD CLEANUP - WOOD FLOORING where we describe removing mold from wood flooring surfaces.
Cleaning mold from wood framing, or wood building sheathing and similar wood surfaces is discussed at MOLD CLEANUP - WOOD FRAMING & PLYWOOD.
Readers should also see the general advice at MOLD CLEANUP GUIDE- HOW TO GET RID OF MOLD
Also see HIDDEN MOLD in FLOOR / SUB-FLOOR.
Also see TRAPPED MOLD BETWEEN WOOD SURFACES for a discussion of the immobility of mold between wood framing and other surfaces,
and see MOLD GROWTH on SURFACES for an index of what mold genera/species are frequently found on various building surfaces and materials.
Mold, Rot, & Odors in a Water-Damaged / Mold-Damaged Wood Floor
Question: do leaks, water damage & wood floor stains mean we have a significan hidden mold problem? Landlord says we need to move out.
I wasn't really sure if I should post this on one of the advice pages due to the length of our story but feel free to if you think it might help someone else in our situation.
June of last year my fiancé found a house for rent through someone she worked with and we decided to go for it due to the large yard because we have multiple pets.
, 'usernamelengthinvalid':'Username must be between 6-16 characters long.' , 'enterfirstname':'Please enter the firstname.' , 'languagealreadyinsystem':'Language already in the system.' , 'passwordlengthinvalid':'Password must be between 6-16 characters long.' , 'bannedwordalreadyinlist':'Banned word is already in the list.'
Bear in mind we live in Arkansas, the magical land of nonexistent tenant rights. Upon moving in we both started noticing seemingly random symptoms (skin issues, headaches, sinus problems, fatigue, etc.)
When we moved in we were informed of a home in one of the kitchen cabinets that was 'caused by rain' but didn't think much of it.
We also had a problem with roaches around the fridge and found a sizeable hole behind the refrigerator which I've attached a photo as well.
Obviously the symptoms only increased in severity and only after an exhaustive online search did I attribute our symptoms to fungal infection. Prescription medication seemed to help at first but it all came back once we ceased the medication.
So in September I stumbled across Inspectapedia and finally made the connection that mold had to be the cause for our problems.
We got a mold test and the results were shocking to say the least. I've attached a picture of the results about the first test and the second test the second time we let sit on the living-room table for the allotted hour and then sealed it exactly is the instructions directed.
When we brought this to our landlords attention they didn't seem all that shocked by the information in fact they seemed like they might have already known about it and didn't show up until November to attempt any repair to the house.
One night I got the bright idea to look at our crawlspace just to see and I've attached a video of what I found.
They showed up pretty quickly after receiving the video and supposedly pumped out the water and fixed the problem according to them. When I confronted them about what was to be done about the existing mold they replied with this text message:
'Take this months rent and find somewhere else to live ASAP, Since it is causing physical symptoms. To get rid of the mold 100%, we will have to gut the house and no one needs to be living there. We will take your deposit and prorate this months rent for however long it takes you to move.'
This is two weeks before Christmas by the way. So we paid our rent because there aren't really a whole lot of places to move to at the moment we've been looking trust me.
We even had a mold remediation expert come in and evaluate the house and said we'd have to move out and they will have to gut the house which is interesting because that's what they said before we even had the expert come in to look at it. We're at our wits end and don't know what to do stop any advice would be greatly appreciated.
My main question I guess is with hardwood floors, is discoloration a bad sign?
I only got a few pictures of the house we're currently looking at. There's a basement which is uncommon in this area and also much more space than we expected however I'm timid about the fact that a lot of it's been painted.
Covering something up kind of painted I think. But here are a few pictures. The state of the floors are what concern me.
- Anonymous by private email 2020/02/04
Reply: your landlord is probably right
Your story and photos are all a 'bad sign' based on the limited information we have at hand, C.H.
- Your landlord says they need to do a gut renovation and repair of the home and that you need to move out
- Your onsite environmental expert said there is significant mold hazard and that you need to move out
- Your photos suggest a history of leaks from above in building walls, and a paint-over without proper removal of moldy materials that may be present in ceilings, walls, floors
- Your medical complaints need to be considered and advised upon by your doctor but certainly sound as if they could be related to a buidling mold contamination hazard
- You should stop dragging your feet
- You may need to clean your own posessions in the process of moving them into a new location
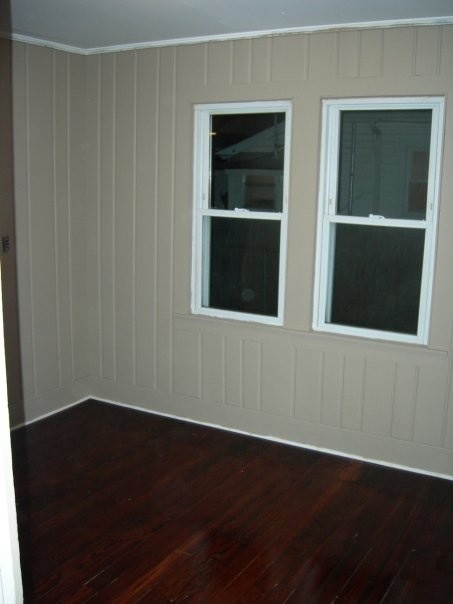
Among your first batch of photos is one of a dish cabinet with badly water-damaged plywood shelving suggesting a history of building leaks from above.
Watch out: the very fact that the damage has been left in place, perhaps painted-over, is a suggestion that any repair work for prior leaks did not address all of the building cavities that have been wet. Wet building insulation or wall cavity side of drywall can present a significant but hidden mold contamination reservoir that can make building occupants sick.
[Click to enlarge any image]
In understanding the significance of stains on a floor we want to make a reasonable guess at the stain cause and thus at the implications for hidden damage, rot, mold, etc. in the building as well as the adequacy of prior repair work.
I can't see a thing in your kitchen floor photo but your first wood floor [annotated above] photos shows dark areas that are distinctly in a pattern originating at a doorway - possibly that's foot traffic or a possible prior leak in the kitchen if that's the doorway involved.
A companion strain to the right and 'around the corner' from doorway No. 1 appears to emanate out of the wall. That's a further hint that there could have been prior leaks in the hidden 'doorway' room or else from above.
Other wood floor photos also show dark stains in traffic areas that could have been from leaks or, less likely by the pattern, animal urine. Were there previously pets in this home?
If there is no visible mold then an expert onsite inspection + building history (of leaks, moisture traps, renovations, repairs) can decide when and where more-invasive inspection for hidden mold reservoirs is justified.
Watch out: however. Though you didn't give details, relying on a 'mold test' alone to screen a building for hidden mold is fundamentally unreliable, not diagnostic, not accurate, and can completely miss problems (false negative results) ; even if such a test suggests that a mold contamination issue is present the molds detected are quite possibly not the problem molds in the building, nor does the test alone give a clue of what to do next.
From the photos it appears to me that there are significant mold reservoirs in this buiding and that someone simply cleaned and painted before re-renting.
Before tackling a moldy or mold-suspect wood floor take a look at
- MOLD / ENVIRONMENTAL EXPERT, HIRE ? - when to hire an expert
Reader Question: how to diagnose a maple syrup smell in room with damaged wood flooring
The owner of a building wants to know why this room smells from maple syrup, the odor is stronger when humidity is high, the wood is maple wood and those blotches seen is not understood, it’s a 100 year old building.
If you can’t make the connection with the information provided what testing do you recommend? - H.G., New York City, 3/20/2014
Reply: sources of sweet maple syrup odors indoors vs. mold damaged floor
I have not come across mold that smells like maple syrup, though consumption of fenugreek as well as other sources have been associated with that odor in buildings. Sweet odors have also been traced to bedbug infestations or cockroach infestations (NYC DOH).
Bees making a colony in a building wall can also be a source of waxy pungent odors. And a few readers have even described sewer gases as 'sweet'.
If the building is framed with cavity walls (not solid masonry) and more if occupants have noticed bees in the area I'd look for a bees nest independent of the apparent rot and fungal decay marks on the floor. Some insecticides or other chemicals applied indoors (perhaps a DIY attempt at mold 'treatment') also give off sweet pungent smells.
Indoor building mold contamination itself is not generally described as making sweet odor but there is indeed such a huge range of mold genera species that no one should assert the presence or absence of a particular odor as mold-related just based on 'opinion'.
There is even a fungus that produces MVOCs that smell like dirty socks.
The stains on the floor look to me like a mix of wood rot and fungal damage that may have been sanded (without repair) and even re-finished.
I add that without an onsite inspection or a physical sample of the light yellow material seen in the flooring gaps I can't say if the material is fungal remains or wood filler (perhaps used to fill in worse rot areas).
It's no surprise that a 100 year old building may have had heating system leaks or other leaks into the floor cavity and floor rot (wood rot is itself a fungal and bacterial action). It's not unheard-of to come across a floor that was re-finished by sanding over rot, filling a few bad spots with wood putty, and coating the new floor.
A close visual inspection that shows that these discolorations were sanded flush and coated-over would argue convincingly for this history.
The pattern of the light yellow material is very strongly suggestive of having filled gaps and areas of rot or other damage with a wood filler product that was then sanded. It is not laid-out in a typical fungal growth pattern.
The pattern of the dark stains could be rot left in place, or other damage at which the surface was concave and not sanded off during floor re-finishing.
I speculate that this is a water-damaged, rotted floor that was sanded and re-finished without pulling up damaged flooring and without cleaning the area below.
Pet Stains on wood floors
Pet urine stains on wood floors - pet stains can ruin wood flooring. Stains are deep enough into the wood that almost no amount of sanding will remove them.
We have had some wood floor stain removal success by careful, by-hand bleaching combined with sanding, followed by careful blending of hand-mixed wood stain products to return the color of the wood floor section to that of its neighbors.
Nail & moisture stains on wood floors
Where small black stains developed in a wood floor in a 1920's bungalow that we restored (our lab and office) we had great success by combining sanding with spot bleach using a Q-tip to lighten the black spots where in prior years moisture had caused bleed and corrosion staining around those fasteners.
Any exposed nails were set into the flooring before sanding. After sanding we sat with a Q-tip and a damp cloth, dabbing and bleaching black spots, wiping and washing off the bleach when the stain was light enough - thus avoiding over-bleaching the floor.
We mixed wood stain products to bring the color of the stained-bleached spots back to the surrounding flooring.
See PET STAINS & MARKS in BUILDING for details including on removing stains from flooring left in place.
Replace Damaged Wood Floor Boards
Details about how to cut out and replace damaged wood floor boards or damaged engineered wood flooring sections are now found
at REPLACE DAMAGED WOOD FLOOR BOARDS - how to cut out and replace badlyh-damaged wood or engineered wood floor boards
[Click to enlarge any image]
It is always smart to use the least-invasive, least-destructive repair or renovation method you can. Floor boards that have been stained, gouged, scratched can often be repaired in place.
Also see WOOD FLOOR ENGINEERED, REPAIRS
Also see LAMINATE FLOOR DAMAGE REPAIR
Also see LAMINATE PLASTIC FLOOR
Surface Scratch Repair on Hardwood Flooring
Here is a long strip solid oak wood floor that's shows ugly but fairly superficial scratches. To make this 1970's strip oak wood floor look perfect, sanding and re-finishing may be necessary.
But an alternative to try first is thorough cleaning, perhaps buffing with steel wool, followed by application of a sealant and finish coating.
Often superficial scratches in a wood floor disappear from view when the scratched finish coating is restored.
It's usually a better practice to repair a floor with the least aggressive means possible, preserving the material for a longer life.
At WOOD FLOOR ENGINEERED, REPAIRS we include research, procedures, and products to repair gouged and scratched hardwood and engineered wood floors.
Diagnose & Repair Water or Solvent Stains on Laminate Flooring
Several of the types of flooring damage discussed above, beginning at BUCKLED WOOD FLOORING due to leaks or high moisture, describe water or moisture damage to floors.
Stains, gaps, buckling, warping and mold are all water-related or moisture-related problems in flooring systems.
At LAMINATE FLOOR DAMAGE REPAIR we add another flooring damage example provided by a reader who included photos of what appears to be a water or solvent-damaged laminted flooring product, probably plastic, not wood.
..
Continue reading at FLOOR, WOOD MOISTURE or select a topic from the closely-related articles below, or see the complete ARTICLE INDEX.
Or see WOOD FLOOR DAMAGE DIAGNOSIS FAQs - questions & answers about this article
Or see these
Related Articles
- FLOOR DAMAGE DIAGNOSIS
- OAK FLOORING NOMA CATALOG 1950 [PDF]
Suggested citation for this web page
WOOD FLOOR DAMAGE REPAIR at InspectApedia.com - online encyclopedia of building & environmental inspection, testing, diagnosis, repair, & problem prevention advice.
INDEX to RELATED ARTICLES: ARTICLE INDEX to BUILDING INTERIORS
Or use the SEARCH BOX found below to Ask a Question or Search InspectApedia
..
Ask a Question or Search InspectApedia
Try the search box just below, or if you prefer, post a question or comment in the Comments box below and we will respond promptly.
Search the InspectApedia website
Technical Reviewers & References
- Simpson, W.T., ed., 'Dry Kiln Opeator's Manual', Agriculture Handbook 188, USDA Forest Service
- Simpson, William, TenWolde, Anton, 'Physical Properties and Moisture Relations of Wood', [PDF] from U.S. FPL, Forest Products Laboratory, Wood Handbook - Wood as an engineering material', 1999, Gen. Tech. Rep. FPL-GTR-113, Madison WI, U.S. Department of Agriculture (USDA) Forest Service, FPL. - retrieved 12/20/2014, original source: http://www.woodweb.com/Resources/wood_eng_handbook/Ch03.pdf
- Skaar, C., Wood Water RElations, 1988, Springer-Verlag, New York 1988
- Stamm, A.J., Loughborough W.K., Thermodynamics of the swelling of wood, Journal of Physical Chemistry 1935, 39(1):121
- America's Favorite Homes, mail-order catalogues as a guide to popular early 20th-century houses, Robert Schweitzer, Michael W.R. Davis, 1990, Wayne State University Press ISBN 0814320066 (may be available from Wayne State University Press)
- American Plywood Association, APA, 'Portland Manufacturing Company, No. 1, a series of monographs on the history of plywood manufacturing',Plywood Pioneers Association, 31 March, 1967, www.apawood.org
- Asbestos products and their history and use in various building materials such as asphalt and vinyl flooring includes discussion which draws on ASBESTOS, ITS INDUSTRIAL APPLICATIONS, ROSATO 1959, D.V. Rosato, engineering consultant, Newton, MA, Reinhold Publishing, 1959 Library of Congress Catalog Card No.: 59-12535 (out of print).
- Best Practices Guide to Residential Construction, by Steven Bliss. John Wiley & Sons, 2006. ISBN-10: 0471648361, ISBN-13: 978-0471648369, Hardcover: 320 pages, available from Amazon.com and also Wiley.com. See our book review of this publication.
- Building Research Council, BRC, nee Small Homes Council, SHC, School of Architecture, University of Illinois at Urbana-Champaign, brc.arch.uiuc.edu. 'The Small Homes Council (our original name) was organized in 1944 during the war at the request of the President of the University of Illinois to consider the role of the university in meeting the demand for housing in the United States. Soldiers would be coming home after the war and would be needing good low-cost housing. .. In 1993, the Council became part of the School of Architecture, and since then has been known as the School of Architecture-Building Research Council. .. The Council's researchers answered many critical questions that would affect the quality of the nation's housing stock.
- How could homes be designed and built more efficiently?
- What kinds of construction and production techniques worked well and which did not?
- How did people use different kinds of spaces in their homes?
- What roles did community planning, zoning, and interior design play in how neighborhoods worked?
- Isham: 'An Example of Colonial Paneling', Norman Morrison Isham, The Metropolitan Museum of Art Bulletin, Vol. 6, No. 5 (May, 1911), pp. 112-116, available by JSTOR.
- Manufactured & Modular Homes: Modular Building Systems Association, MBSA, modularhousing.com, is a trade association promoting and providing links to contact modular builders in North America. Also see the Manufactured Home Owners Association, MHOAA, at www.mhoaa.us. The Manufactured Home Owners Association of America is a National Organization dedicated to the protection of the rights of all people living in Manufactured Housing in the United States.
- Pergo AB, division of Perstorp AB, is a Swedish manufacturer or modern laminate flooring products. Information about the U.S. company can be found at http://www.pergo.com where we obtained historical data used in our discussion of the age of flooring materials in buildings.
- Plank House Construction: webslog from plankhouse.wordpress.com/2009/01/25/plank-house-construction/ and where plank houses were built by native Americans, see
Large 1:6 Scale Plank House Construction / P8094228, Photographer: Mike Meuser
06/12/2007 documented at yurokplankhouse.com where scale model Museum quality Yurok Plank Houses are being sold to raise money for the Blue Creek - Ah Pah Traditional Yurok Village project. - Simpson, W.T., ed., 'Dry Kiln Opeator's Manual', Agriculture Handbook 188, USDA Forest Service
- Simpson, William, TenWolde, Anton, 'Physical Properties and Moisture Relations of Wood', [PDF] from U.S. FPL, Forest Products Laboratory, Wood Handbook - Wood as an engineering material', 1999, Gen. Tech. Rep. FPL-GTR-113, Madison WI, U.S. Department of Agriculture (USDA) Forest Service, FPL. - retrieved 12/20/2014, original source: http://www.woodweb.com/Resources/wood_eng_handbook/Ch03.pdf
- Skaar, C., Wood Water RElations, 1988, Springer-Verlag, New York 1988
- Stamm, A.J., Loughborough W.K., Thermodynamics of the swelling of wood, Journal of Physical Chemistry 1935, 39(1):121
- Weaver: Beaver Board and Upson Board: Beaver Board and Upson Board: History and Conservation of Early Wallboard, Shelby Weaver, APT Bulletin, Vol. 28, No. 2/3 (1997), pp. 71-78, Association for Preservation Technology International (APT), available online at JSTOR.
Books & Articles on Building & Environmental Inspection, Testing, Diagnosis, & Repair
- Our recommended books about building & mechanical systems design, inspection, problem diagnosis, and repair, and about indoor environment and IAQ testing, diagnosis, and cleanup are at the InspectAPedia Bookstore. Also see our Book Reviews - InspectAPedia.
- ASTM F 1637, Standard Practice for Safe Walking Surfaces, (Similar to the above standards)
- ASHRAE resource on dew point and wall condensation - see the ASHRAE Fundamentals Handbook, available in many libraries.
- Best Practices Guide to Residential Construction, by Steven Bliss. John Wiley & Sons, 2006. ISBN-10: 0471648361, ISBN-13: 978-0471648369, Hardcover: 320 pages, available from Amazon.com and also Wiley.com. See our book review of this publication.
- ..
- Carson, Dunlop & Associates Ltd., 120 Carlton Street Suite 407, Toronto ON M5A 4K2. Tel: (416) 964-9415 1-800-268-7070 Email: [email protected]. The firm provides professional HOME INSPECTION SERVICES and also extensive HOME INSPECTION EDUCATION and home inspection-related PUBLICATIONS. Alan Carson is a past president of ASHI, the American Society of Home Inspectors.
Thanks to Alan Carson and Bob Dunlop, for permission for InspectAPedia to use text excerpts from The Home Reference Book & illustrations from The Illustrated Home. Carson Dunlop Associates' provides extensive home inspection education and report writing material.
The ILLUSTRATED HOME illustrates construction details and building components, a reference for owners & inspectors.
Special Offer: For a 5% discount on any number of copies of the Illustrated Home purchased as a single order Enter INSPECTAILL in the order payment page 'Promo/Redemption' space.
TECHNICAL REFERENCE GUIDE to manufacturer's model and serial number information for heating and cooling equipment, useful for determining the age of heating boilers, furnaces, water heaters is provided by Carson Dunlop Weldon & Associates
Special Offer: Carson Dunlop Associates offers InspectAPedia readers in the U.S.A. a 5% discount on any number of copies of the Technical Reference Guide purchased as a single order. Just enter INSPECTATRG in the order payment page 'Promo/Redemption' space. - The HOME REFERENCE BOOK - the Encyclopedia of Homes, Carson Dunlop & Associates, Toronto, Ontario, 25th Ed., 2012, is a bound volume of more than 450 illustrated pages that assist home inspectors and home owners in the inspection and detection of problems on buildings. The text is intended as a reference guide to help building owners operate and maintain their home effectively. Field inspection worksheets are included at the back of the volume.
Special Offer: For a 10% discount on any number of copies of the Home Reference Book purchased as a single order. Enter INSPECTAHRB in the order payment page 'Promo/Redemption' space. InspectAPedia.com editor Daniel Friedman is a contributing author.
Or choose the The HOME REFERENCE eBook for PCs, Macs, Kindle, iPad, iPhone, or Android Smart Phones.
Special Offer: For a 5% discount on any number of copies of the Home Reference eBook purchased as a single order. Enter INSPECTAEHRB in the order payment page 'Promo/Redemption' space. - Building inspection education & report writing systems from Carson, Dunlop & Associates Ltd
COMMERCIAL BUILDING INSPECTION COURSES - protocol ASTM Standard E 2018-08 for Property Condition Assessments
HOME INSPECTION EDUCATION COURESES (Canada)
HOME INSPECTION EDUCATION COURSES (USA) including home study & live classes at eleven colleges & universities.
HOME INSPECTION EDUCATION: HOME STUDY COURSES - ASHI@Home Training 10-course program.
Special Offer: Carson Dunlop Associates offers InspectAPedia readers in the U.S.A. a 5% discount on these courses: Enter INSPECTAHITP in the order payment page 'Promo/Redemption' space. InspectAPedia.com editor Daniel Friedman is a contributing author. - The Horizon Software System manages business operations,scheduling, & inspection report writing using Carson Dunlop's knowledge base & color images. The Horizon system runs on always-available cloud-based software for office computers, laptops, tablets, iPad, Android, & other smartphones
If a portion of wall paneling has lifted or buckled, you can fix it. Hammer a few nails into the groove where it’s buckled. If the extra nails hold it flat, countersink them and fill the surface with a premixed wood putty.
If the panel still pulls up, take the panel off the wall and reglue it. You need a putty knife, pliers, wood adhesive, a hammer, paneling or finish nails, and a touch-up stick. Here’s what to do:
Use a stiff putty knife to lift the panel.
Press the panel back down and pull out the nails.
They should be easy to get at if you lift the panel first.
Apply the adhesive to exposed studs, furring strips, or the drywall.
Furring strips are narrow strips of wood used either to raise the surface, level the surface, or otherwise smooth out a rough surface to prepare it for paneling.
Let the adhesive sit and then push the panel firmly against the adhesive.
The adhesive should feel thick but sticky before you try to reattach the panel.
Nail the panel in place by starting in the center and working outward.
Sink the nails into the grooves as much as possible; they won’t be as noticeable there. Use the touch-up stick to hide scratches or the nail heads, if necessary.
If any adhesive comes out of the seams, and it cleans up in water, wipe it off immediately with soapy water.
If you’re using an oil-based adhesive, leave it in place until it until it dries, then cut it off with a utility knife.